Low Pressure Turbine Bypass
Application Discussion
AD120
June 15, 2003
During startup, shutdown and load disturbances in a power plant, the boiler (HRSG in combined cycle designs) and steam turbine need to be isolated from one another. This is to protect the turbine from any water carry over, but also protect additional plant equipment from large thermal transients. By isolating the boiler and steam turbine it is also possible to reduce fuel consumption during startup and shutdown. In the event of a load rejection, reloading times can also be improved through the turbine bypass system.
The turbine bypass system is designed to provide the quickest startup time by controlling both boiler pressure and temperature. Bypassing the steam around the turbine allows the steam to attain the desired qualities before being routed through the turbine. If the turbine bypass system were not used, the firing rate of the boiler would have to be reduced, which could lead to tube failures. The bypass system allows the boiler to be fired at full capability without introducing large thermal gradients in the thick walled components such as the boiler drum and any separators or flash tanks.
Figure 1 shows a conventional power cycle with single reheat capability. In order to protect the reheater tube banks from overheating, the high pressure steam is routed around the high pressure turbine into the cold reheat piping. The steam flows through the reheater tube banks and is then routed through the low pressure turbine bypass valve to the condenser. This type of arrangement ensures that the boiler can remain in operation during a load rejection, which keeps the safety valves from lifting, and keeps other equipment from tripping allowing immediate reloading of the turbine.
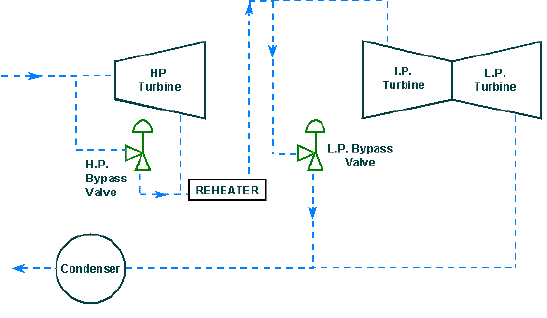
Figure 1: Single Reheat Turbine Bypass System
In conventional units and combined cycle units without hot reheat bypass valves, the low pressure valve must be able to bypass the entire unit mass flow in the case of an upset. Also, the temperature of the steam must be reduced to near saturated conditions to limit the size of the condenser and prevent thermal fatigue due to high temperatures.
One of the main concerns in this application is the noise generated when the pressure is let down from the low pressure section (75 - 200 psig) to the condenser, which is under vacuum (2 – 5 psia). The noise generated can cause vibration that can damage the downstream equipment.
Another concern is temperature control. Inlet temperatures to the valve vary between 400 and 600 degrees and must be dropped to near saturated conditions at the valve outlet. This is necessary to facilitate heat transfer in the condenser while protecting the condenser from thermal fatigue.
For the best efficiencies and overall plant heat rate, tight shutoff is recommended. If the bypass valve leaks, steam that could be driving the turbine will be lost to the condenser. Because of the pressures and the large amount of flow involved, poor shutoff will lead to significant valve damage in a relatively short amount of time.
There are several possible solutions to address this application. The most common device used is called a turbine bypass valve that combines both pressure and temperature reduction into one control valve. The valve controls the flowing pressure drop the same as any control valve, but controls the temperature via a spray water section at the exit of the valve. This spray water section can either be attached to the valve or some distance downstream.
Another alternative is a separate pressure reducing valve and a separate desuperheater downstream from the valve. This arrangement works well when installation flexibility is a consideration. The downside is that if the valve and desuperheater are separated a deadtime or lag can be introduced into the system because of the distance between the pressure reducing valve and downstream cooling section.
Fisher recommends the use of the Fisher CON-TEK CVX valve design. This turbine bypass valve incorporates both pressure and temperature control into one valve body. The valve is designed to withstand the thermal transients typical in this application. Included in this design is extensive research into thermal mixing of water and steam ensuring the best spray patterns and nozzle designs on the market.
For applications where installation flexibility is required, the Fisher design EW or FB with a downstream cooler or desuperheater is recommended. Noise abatement trim can be installed into the control valves to eliminate any damaging noise and vibration. The same type of cooler used with the CVX design can be installed a given distance downstream of the pressure reducing valve to provide the proper temperature control.
Fast acting actuation is required to protect the steam turbine during the event of a load rejection with most requirements ranging between one and two seconds. The Fisher pneumatic actuation system with the 2625 booster arrangement will meet stroking requirements of one to two seconds. In applications where faster acting times are required, electro-hydraulic actuation packages are available.
To maintain tight shutoff at high temperatures, Fisher recommends the use of the C-seal tight shutoff trim. This trim provides Class V shutoff at temperatures up to 1100 degrees. The true balanced construction minimizes actuator force requirements and eliminates problems with installation, setup and removal. |